Contact an HP 3D Print expert
Choose the phone number for your country to speak to a local HP 3D Printing sales expert today.
België/Belgique
Czech Republic
Deutschland
España
France
Italia
Nederland
Norway
Österreich
Poland
Romania
Sweden
Suisse/Switzerland
United Kingdom
United States
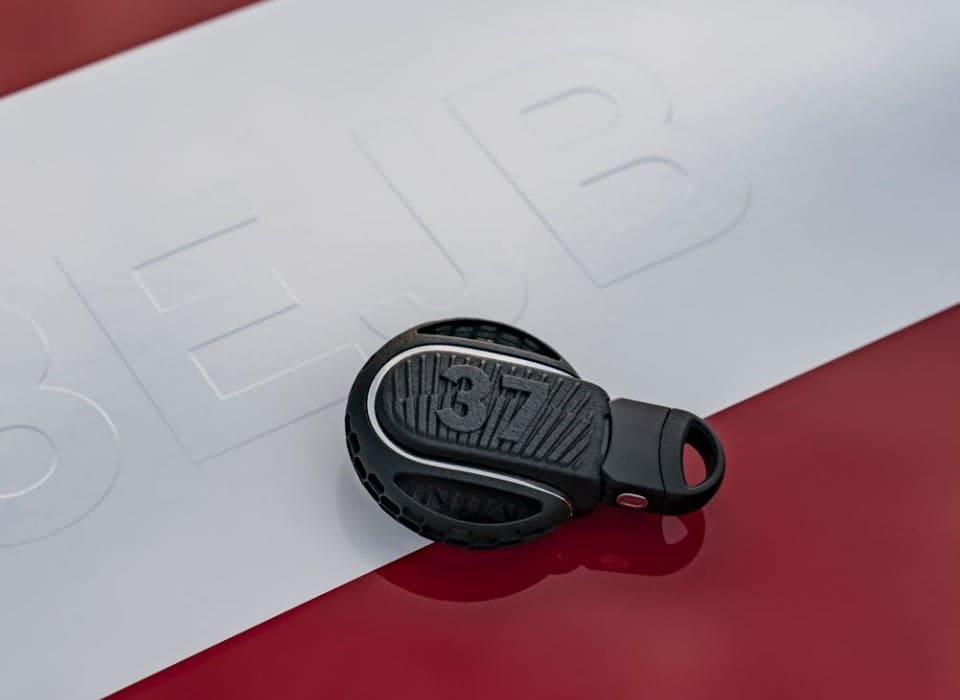
3D printed keycaps are a turn-on for automotive customers
Custom 3D printing solutions from HP enable manufacturers to develop unique and appealing car accessories.
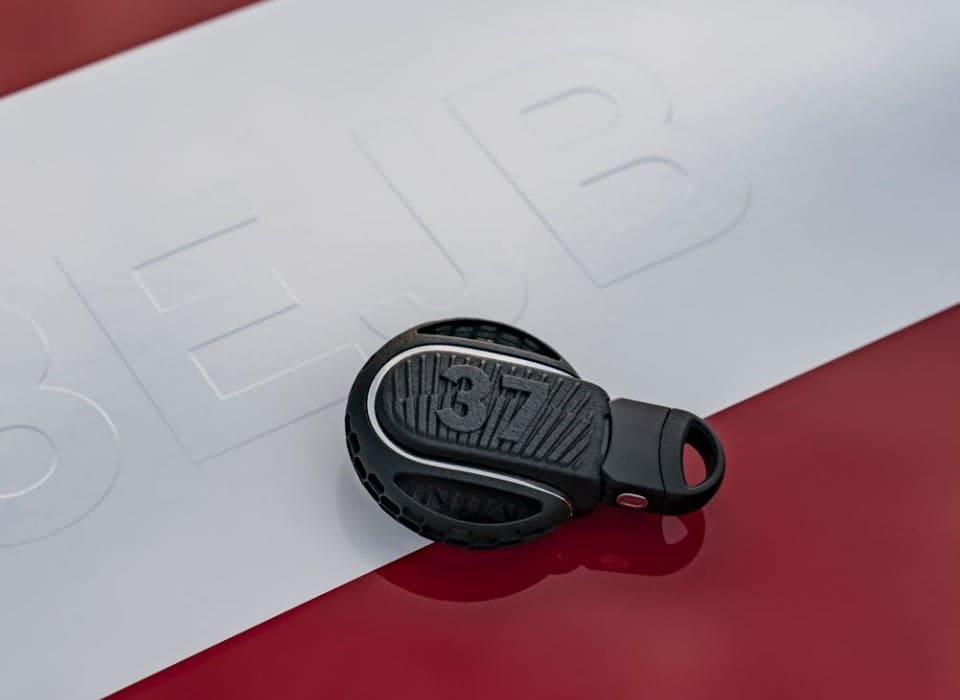
Data courtesy1
Custom 3D printing services for the automotive industry
Additive manufacturing solutions are having a major impact on the automotive industry. The technology offers several advantages over traditional manufacturing methods. Depending on the application, 3D printing can be faster, more flexible, and less costly. It also unlocks new design freedom which helps optimize parts and reduce weight and complexity. Further, 3D printing is digital, which not only enables high-value customized and personalized parts, but also reduces waste, creating a sustainability advantage.
In the past, 3D printing for transportation was primarily used for prototyping. It allowed engineers to create mock-ups of parts and assemblies faster and more easily than they could with other methods. But as the technology has improved, car manufacturers began using it for tooling - including jigs and fixtures - that reduce the time involved with mass manufacturing. More recently, automakers began using 3D printing for cars to create a variety of end-use parts including interior trim, engine components, accessories, and even spare parts for their vehicles.
3D printed car parts including automotive accessories
Custom 3D printing services are evolving rapidly in the automotive industry and are now being used to manufacture many types of accessories, including cup holders, clips, knobs, hooks, and aerodynamic components, among other 3D printed car parts.
Custom 3D printing offers many benefits for accessory manufacturers, including:
- Novel design: design freedom allows product developers to create new, geometrically complex parts with fine detail that improve performance or reduce assembly costs.
- Customization: Consumers are looking for ways to make their cars unique and reflect their personal style. This trend is being driven by a number of factors, including the increasing availability of digital technology that enables limited editions of very few exclusive designs, ultimately moving towards “audience of one” applications.
- Shorter lead times: In an environment where production is typically planned months or years in advance, 3D printing can deliver parts in hours or days. Because of this, parts can be manufactured just in time or even, on demand. Moreover, 3D printing enables car makers to overcome supply chain disruptions thanks to its bridge production capability.
- Fewer errors: the digital process allows consumers to view a visual “proof” and eliminates the potential for mistakes in production.
Auto makers differentiate with 3D printed artisan keycaps
Custom and limited 3D keycap editions are a great way for consumers to personalize the driving experience. 3D printed keycaps can be manufactured in unique shapes and colors, and can be embossed with text and images, which can be chosen or supplied by the user. 3D printed keycaps can also be more durable than traditional keyfobs or PLA keycaps, and can be easily replaced if lost or damaged.
BMW 3D print collaboration unveils limited edition keycaps
Recently, BMW Group partnered with HP to 3D print custom keycaps for limited edition versions of the iconic MINI Cooper. The BMW 3D print collaboration was announced at the 2022 Consumer Electronics Show (CES) in Las Vegas. The 3D printed artisan keycaps were customized with an image related to each limited edition and in one example, a unique treatment of the MINI logo.
Data courtesy1
The keycaps were made using HP’s Multi Jet Fusion (MJF) 3D Printing technology and HP 3D High Reusability (HR) PA 11 material. This custom 3D printing solution provided the surface finish and strength required for a finished part, and the material’s bio-based origin contributed towards sustainability objectives. HP 3D HR PA 11 is a 100% bio-based polymer made from castor oil, which helps achieve corporate social responsibility goals. The keycaps were easy to assemble and could also be swapped out as needed.
To read more about how BMW Group produced custom 3D printed keycaps faster and less expensively, please view the case study.
Volkswagen manufactures custom metal 3D printed keycaps
In 2018, Volkswagen and HP announced a partnership to develop 3D printing technologies for car accessories. The partnership focused on developing metal 3D printing capabilities that can be used to produce high-quality, lightweight, and durable car accessories. Many different items have been produced thus far, including customized nameplates, keycaps, 3D printed shift knobs, and more.
Data courtesy2
Utilizing HP’s Metal Jet technology enabled Volkswagen mass production in a very short amount of time. HP’s 3D printing process also allowed them to manufacture 3D parts without the need for molds and other manufacturing tools.
To see how HP’s Metal Jet 3D printing enabled VW to manufacture 3D printed keycaps and other car accessories more quickly and less expensively, watch the video.
Peugeot takes 3D printing for cars to a whole new level
In 2021, Peugeot partnered with HP to manufacture a range of car accessories for the Peugeot 308. The accessories included a sunglasses holder, a can holder, and a phone/card holder. The accessories were made from BASF Ultrasint TPU01 thermoplastic polyurethane (TPU) material that is durable, lightweight, and easy to clean.
Data courtesy3
The 3D printed car accessories were the result of a joint effort between Peugeot, HP, Mäder, and ERPRO. Production was accomplished using HP’s Jet Fusion 3D Printing Solution, and the items were designed to be pleasant to the touch and easy to use, while also being light, solid, and durable.
Some of the benefits were achieved thanks to the design freedom enabled by 3D printing, which allowed engineers to create parts that were lighter, stronger, and more flexible. HP’s MJF technology expanded the advantage, allowing Peugeot to pursue customization, shorter lead times, and “on-demand” production.
Additionally, since 3D printing is not subject to minimum order quantities, it enabled Peugeot to produce these accessories in multiple colors and shapes, hence offering customers a wider range of choices compared to traditional manufacturing methods where large volumes are required for the same design.
To learn more about Peugeot’s line of 3D printed car accessories, and how HP MJF 3D printing made them more flexible and sustainable, read the case study.
Learn more about 3D printing for transportation
Interested in learning more about manufacturing 3D printed keycaps and other 3D printed car parts? Explore the library with use cases on automotive and transportation or contact an expert and learn how you can benefit from custom 3D printing with HP.
Want to continue learning?
Footnotes and disclaimers
- Data courtesy of BMW Group
- Data courtesy of Volkswagen Group
- Data courtesy of Peugeot
Select Your Country/Region and Language
Close Country/Region Selector Dialog- Africa
- Afrique
- België
- Belgique
- Česká republika
- Danmark
- Deutschland
- Eesti
- España
- France
- Hrvatska
- Ireland
- Italia
- Latvija
- Lietuva
- Magyarország
- Middle East
- Nederland
- Nigeria
- Norge
- Österreich
- Polska
- Portugal
- România
- Saudi Arabia
- Slovenija
- Slovensko
- South Africa
- Suisse
- Suomi
- Sverige
- Switzerland
- Türkiye
- United Kingdom
- Ελλάδα
- България
- Казахстан
- Србија
- Україна
- ישראל
- الشرق الأوسط
- المملكة العربية السعودية
HP Worldwide
Select Your Country/Region and Language
- Africa
- Afrique
- América Central
- Argentina
- Asia Pacific
- Australia
- Bangladesh
- België
- Belgique
- Bolivia
- Brasil
- Canada
- Canada - Français
- Caribbean
- Česká republika
- Chile
- Colombia
- Danmark
- Deutschland
- Ecuador
- Eesti
- España
- France
- Hong Kong SAR
- Hrvatska
- India
- Indonesia
- Ireland
- Italia
- Latvija
- Lietuva
- Magyarország
- Malaysia
- México
- Middle East
- Nederland
- New Zealand
- Nigeria
- Norge
- Österreich
- Pakistan
- Paraguay
- Perú
- Philippines
- Polska
- Portugal
- Puerto Rico
- România
- Saudi Arabia
- Singapore
- Slovenija
- Slovensko
- South Africa
- Sri Lanka
- Suisse
- Suomi
- Sverige
- Switzerland
- Türkiye
- United Kingdom
- United States
- Uruguay
- Venezuela
- Việt Nam
- Ελλάδα
- България
- Казахстан
- Србија
- Україна
- ישראל
- الشرق الأوسط
- المملكة العربية السعودية
- ไทย
- 中华人民共和国
- 臺灣 地區
- 日本
- 香港特別行政區
- 한국
- Recalls|
- Product recycling|
- Accessibility|
- CA Supply Chains Act|
- Privacy|
- Use of cookies|
- Your privacy choices|
- Terms of use|
- Limited warranty statement|
- Terms & conditions of sales & service|
©2024 HP Development Company, L.P. The information contained herein is subject to change without notice.