Data courtesy1
Interested in other articles?
Interested in other articles?
Additive manufacturing has evolved significantly in recent years. In the past, it was expensive and slow, limiting its use primarily for mockups and prototypes. Today, advancements in 3D printing technology, a wide choice of materials, and game-changing economics are causing manufacturers to consider new use cases, including innovative 3D manufacturing of end-use parts.
How does innovative 3D printing make the difference?
Recent 3D printing innovations have enabled solutions that are faster, less expensive, and offer a wide portfolio of engineering-grade materials, making them flexible enough to support part manufacturing from prototyping to production. Modern 3D printing systems empower product teams, allowing them to experiment with new geometries, quickly develop new parts, and radically improve existing designs without the time and expense of tooling and other fixed costs associated with traditional processes. Further, efficient short-run economics allows companies to customize their offerings, manufacture in smaller batches, and reduce part inventories.
Who is innovating with 3D printing?
The most innovative 3D printing companies work in many different industries, including automotive, healthcare, and consumer goods, among others. Many of them rely on HP’s Multi Jet Fusion (MJF) 3D printing technology. Here are just a few examples of their award-winning, innovative 3D manufacturing successes:
3D printing innovations at GM
General Motors has developed many 3D printing innovations with HP’s MJF technology. Recently, for example, they used the solution to manufacture closeout seals for the spoilers of some of their most popular SUVs. Working with HP and GKN Forecast 3D, they were able to streamline their additive manufacturing process, enabling them to produce and finish 60,000 parts over the span of five weeks. Using conventional processes, the parts would have taken significantly longer and delayed production. In contrast, innovative 3D printing allowed them to accelerate the scheduling of 30,000 vehicles.
Why was there a rush on the parts? According to GM engineers Adam Campbell and Christine Bardsley, an engineering change was made as GM was preparing the production line for its new 2022 models. The decision required a new part, which is very unusual so late in the product development process.
Instead of using traditional processes, which would have delayed customer deliveries, the additive manufacturing team at GM’s Additive Industrialization Center developed an innovative 3D manufacturing solution using HP MJF that allowed them to design and produce 3D printed parts that are both aesthetically and functionally comparable to similar injection molded parts.
With an innovative 3D printing solution in place, engineers at GM quickly designed the new part and conducted wind tunnel testing to ensure the part met aerodynamic specifications. Then they enlisted the support of GKN Forecast 3D to accelerate the finishing process. Within a few days, GKN Forecast 3D identified, tested, and validated an innovative 3D manufacturing technique that reduced the time it would have taken to surface finish the parts by 60%. With the time saved, the teams were able to accelerate their production schedule, saving GM time and cost, while eliminating the risk of production delays.
GM’s innovative 3D printing application was recently named the Award Winner at the 2022 SPE Automotive Innovation Awards and Gala. See more about their entry here.
Read the full article to learn more about how GM is innovating with 3D printing and their future plans for the technology.
FITED uses innovative 3D manufacturing to treat scoliosis
Auto makers aren’t the only ones innovating with 3D printing. The healthcare industry has also adopted innovative 3D printing technologies to enable customization and radically enhance product design, improving patient outcomes.
Scoliosis is a genetic disease that affects 4% of the worldwide population. It causes a sideways curvature of the spine that occurs most often just before puberty. Scoliosis braces are a non-invasive treatment and are preferred for children due to risks involved with invasive spine surgery. Studies have shown that scoliosis braces can be an effective treatment, eliminating the need for surgery for as many as 72% of patients.
Current scoliosis braces are hand-made from thermoformable polymers and are poorly constructed, bulky, and painful for most juvenile patients. Social stress, psychological impact, and reduced daily activity contribute to noncompliance in pediatric patients. In fact, studies show just 14.5% wear the devices as intended.
FITED is dedicated to fighting scoliosis with technology. Their 3D printed scoliosis braces offer better results, enhanced patient comfort, and compliance, all within a beautiful, lightweight design. They are manufactured using HP’s MJF 3D printing technology, and their innovative 3D manufacturing solution is designed to boost compliance and improve treatment outcomes while eliminating patient pain, expense, and production time. FITED Braces are low-profile and anatomically exact, allowing patients to maintain regular activities while the device is hidden beneath clothing. This improves the scoliosis patient's living conditions and reduces the trauma associated with wearing bulky devices.
Data courtesy2
With such a novel approach to scoliosis brace design, FITED has demonstrated they are one of the most innovative 3D printing companies, and they have the accolades to prove it. In 2022, their device was named Health Category Platinum Winner at the SPARK Awards. Also in 2022, FITED received a European Product Design Award, and they were named the Top Design Winner in Life Science Design/Aids/Prosthetics.
HILOS develops innovative 3D printing solution for shoes
HILOS began with a group of designers, engineers, and artists who questioned how shoes were being made with the hopes of doing better. In their research, they found that 24 billion shoes are made each year and that making them requires 48 trillion gallons of fresh water. They also learned that one in five shoes goes straight to the trash without ever being worn.
HILOS decided to reinvent shoe manufacturing by blending digital design with innovative 3D manufacturing and artisan craftsmanship to produce personalized footwear that is made locally and sustainably.
A 3D printed and completely recyclable shoe represents an evolutionary step for the footwear industry. Just a few years ago, 3D printing innovations like this seemed impossible. But with recent advancements in hardware, software, and materials, HILOS was ready to accept the challenge.
HILOS launched The Georgia in May 2021 to showcase the possibilities of innovative 3D printing. The Georgia combines a traditional insole, midsole, & outsole into a single 3D-printed platform. A digital mesh lattice cushion provides all day comfort, outperforming traditional footwear solutions. Internal geometries and architectural structures hold the upper in place with a steel cable, allowing for ease of disassembly and recyclability. Each pair is made on-demand within 72 hours from click-to-ship, eliminating overproduction, while saving 1,700 gallons of water for every pair made.
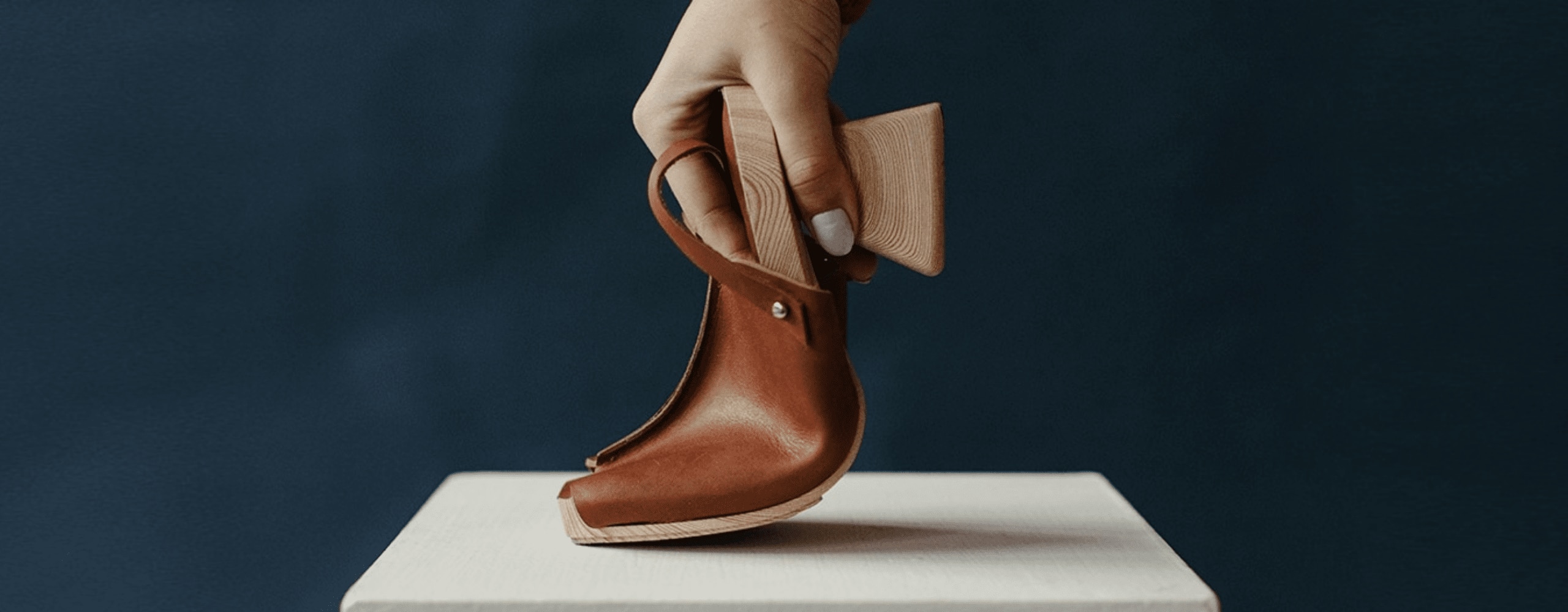
Data courtesy1
For its efforts, HILOS also won a SPARK Award, taking home the Gold prize in the Consumer Products category. In addition, HILOS was also recognized by the Global Footwear Awards, winning in the “Other Sustainable Manufacturing Process” category.
OECHSLER upgrades the automotive seating experience
Founded in 1864, OECHSLER, AG has become a leading polymer technology company, supplying customers worldwide in the automotive, sporting goods, healthcare, and innovative technology sectors. As a turnkey partner for its customers, OECHSLER provides design and development capabilities and innovative 3D printing with a fleet of devices that can support low and high-volume production needs.
The company recently utilized its innovative 3D manufacturing process to develop and produce automotive upholstery that is individually adapted to the needs of the user. Their lightweight, performance-oriented, automotive seat pads offer enhanced ventilation and breathability while also providing the ideal damping properties needed for various uses.
OECHSLER’s engineers began by creating unique pressure maps that measure body geometries and utilized design for additive manufacturing (DfAM) to convert them into lattice structures. After extensive simulation and real-world testing, they were able to develop customized seating pads that are lighter and reduce peak pressure points and dissipate heat better than automotive foam.
Data courtesy3
OECHSLER leveraged HP’s innovative 3D printing technology to produce these functional and flexible parts. They also utilized BASF’s Ultrasint® TPU01 material, which is approved for skin contact (ISO 10993/ OECD No.439), tested for durability (fatigue bending ASTM D1052) as well as flame resistance (FMVSS 302), chemical resistance, and UV resistance (ISO 4892-2A Cycle 1).
For their efforts, OECHSLER also received a European Product Design Award in 2022, winning in the Transportation/Auto Accessories and Interiors category.
The magic behind innovative 3D manufacturing
The common denominator behind all of these award-winning applications is MJF 3D printing technology. Not surprisingly, HP has also received its share of honors. In 2022, the HP Jet Fusion 5200 3D printing solution was named the Enterprise 3D Printer of the Year for polymers.
Want to get ahead with innovative 3D printing?
Contact an HP 3D printing expert to learn how you can use innovative 3D manufacturing to design and produce award-winning, high-value parts that enhance your product’s capabilities and extend your competitive advantage.
Want to continue learning?
Next article
Related article
Related content
Footnotes and disclaimers
- Data courtesy of HILOS
- Data courtesy of FITED
- Data courtesy of OECHSLER