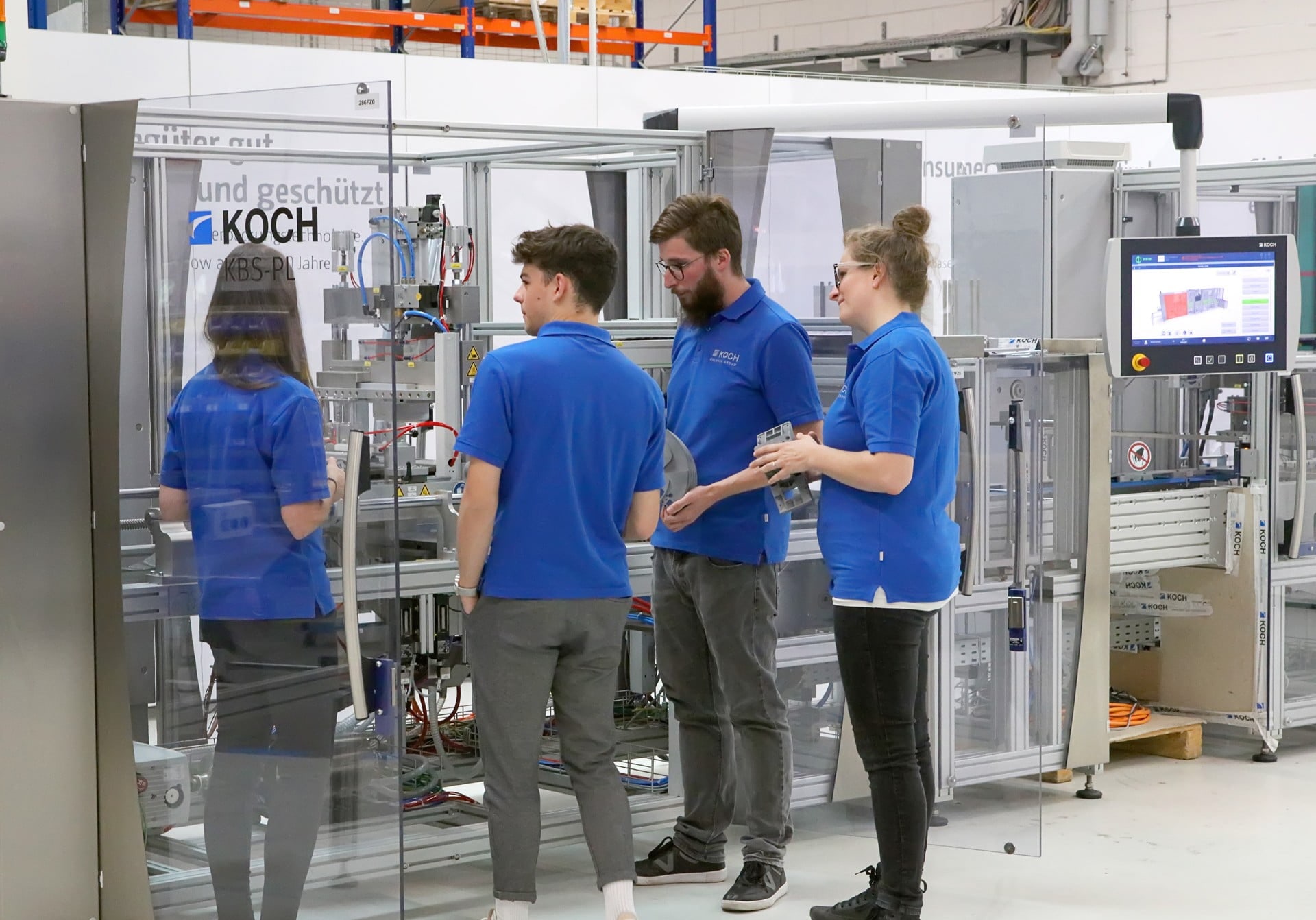
3D printing for manufacturing customized machinery parts
3D printing for manufacturing customized machinery parts
KOCH Pac-Systeme revolutionizes machinery production with 3D printing for manufacturing of machinery parts.
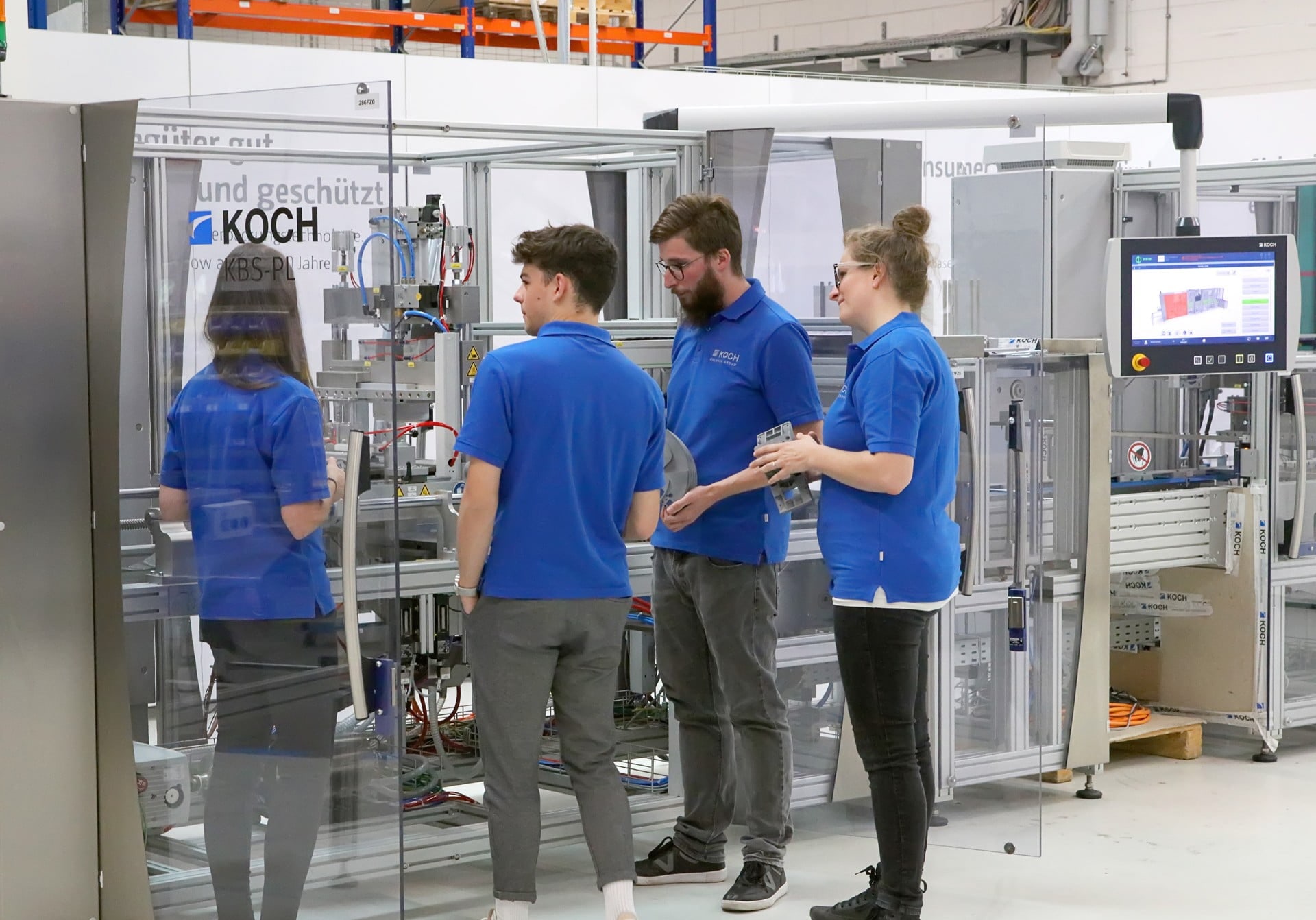
Data courtesy1
Quick facts
Industry
Materials
Challenge
To produce cost-efficient, customized and sustainable packaging machinery parts and to meet increasing customer demands, including higher cycle rates and product quality, all while lowering material consumption.
Technology
Results
For ten years, KOCH Pac-Systeme used external 3D printing manufacturers to create parts. Recently, they installed an HP Jet Fusion 3D printer and now produce parts in-house, faster and more cost effectively.
CHALLENGE
Accelerating design and production of complex machinery parts
KOCH Pac-Systeme is a leading global manufacturer of blister machines, cartoners and packaging lines for a range of industries including consumer goods and healthcare.
Utilizing the latest in modular design, each blister machine, cartoner and packaging line can be individually configured and customized according to a customer’s specifications. This means that production requires many complex and unique parts to be developed, often in small or even one-off production runs.
These parts were previously made with traditional manufacturing, for example, injection molding. However, traditional manufacturing was expensive, time-intensive, inflexible and unable to create some of the complex geometries required.
KOCH Pac-Systeme needed to find a new production method that would allow them to create complex parts for low cost and at speed, all while allowing them to rapidly prototype their designs and optimize without significant delay to their overall production.
Data courtesy1
SOLUTION
HP MJF delivering on speed, production, agility, and flexibility
As a driver of innovation, KOCH Pac-Systeme is constantly assessing new technologies that might improve its production processes. And like many companies, they’re used to balancing the best technological solution with the approach that is most cost-effective.
With HP Multi Jet Fusion (MJF) technology, they didn’t have to choose. This technology was both the best solution available and the most cost-effective.
By utilizing HP Jet Fusion 3D Printing in production, KOCH Pac-Systeme can create designs without limitations and develop solutions that would not have been possible using traditional manufacturing processes. HP Multi Jet Fusion technology enables the production of 3D printed machinery parts that are lighter, more complex, and at the same time more cost-effective.
All of this is achieved while allowing for greater speed, production agility and flexibility at all phases of production. In addition, the ability for 3D printed production parts to be designed, developed and prototyped in-house adds agility and, most importantly, increased customer satisfaction.

"We’ve worked out that, in the case of very small components, the kind that we need in quantities of 10 to 100, there’s a saving of up to 10 times what conventional milled parts would cost. Additive manufacturing has also provided us with much better options in terms of scope for creative design."
"We’ve worked out that, in the case of very small components, the kind that we need in quantities of 10 to 100, there’s a saving of up to 10 times what conventional milled parts would cost. Additive manufacturing has also provided us with much better options in terms of scope for creative design."
Jürgen Bitzer, Director, Corporate Engineering, KOCH Pac-Systeme

Data courtesy1
RESULTS
A 3D printing manufacturing solution to drive innovation forward - fast
Having the HP Jet Fusion 3D Printer has brought new levels of design freedom and fewer production-related limits to KOCH Pac-Systeme. Engineers can have an idea, draw a plan, and print the part directly without using external producers.
"In manufacturing special-purpose machines, every system is a one-off. And often, we have to optimize components at the very last minute. Having access to this technology in-house, we have the opportunity to test out new versions of parts overnight."
Jürgen Bitzer, Director, Corporate Engineering,
KOCH Pac-Systeme
The company currently uses over 100 HP MJF 3D manufactured machinery parts in the blister machines and packaging lines.
Take, for example, their award-winning KBS-C medplus blister machine system, which is composed of three basic modules, each one made up of 40 HP MJF printed components, some of which are extremely intricate. Producing these parts with traditional manufacturing would entail creating multiple screws, connections, tubes and switches, which would make the production and installation overly complicated.
Data courtesy1
Data courtesy1
Data courtesy1
With HP MJF, it’s easy to print geometries that would otherwise be impossible, such as the casing hiding the door switches which, at only 0.5mm thick, allows the door switch behind to function properly. These parts are not available for purchase and custom manufacturing using conventional production methods would be prohibitively expensive.
HP MJF has become an indispensable part of the KOCH Pac-Systeme production process and is helping to drive the evolution of this innovative company forward.
Interested in knowing more about HP 3D Printing Solutions?
Data courtesy1
Footnotes and disclaimers
- Data courtesy of KOCH Pac – Systeme.
- HP Jet Fusion 3D Printing Solutions using HP 3D High Reusability PA12 provide up to 80% powder reusability ratio, producing functional parts batch after batch. For testing, material is aged in real printing conditions and powder is tracked by generations (worst case for reusability). Parts are then made from each generation and tested for mechanical properties and accuracy.
Select Your Country/Region and Language
Close Country/Region Selector Dialog- Africa
- Afrique
- België
- Belgique
- Česká republika
- Danmark
- Deutschland
- Eesti
- España
- France
- Hrvatska
- Ireland
- Italia
- Latvija
- Lietuva
- Magyarország
- Middle East
- Nederland
- Nigeria
- Norge
- Österreich
- Polska
- Portugal
- România
- Saudi Arabia
- Slovenija
- Slovensko
- South Africa
- Suisse
- Suomi
- Sverige
- Switzerland
- Türkiye
- United Kingdom
- Ελλάδα
- България
- Казахстан
- Србија
- Україна
- ישראל
- الشرق الأوسط
- المملكة العربية السعودية
HP Worldwide
Select Your Country/Region and Language
- Africa
- Afrique
- América Central
- Argentina
- Asia Pacific
- Australia
- Bangladesh
- België
- Belgique
- Bolivia
- Brasil
- Canada
- Canada - Français
- Caribbean
- Česká republika
- Chile
- Colombia
- Danmark
- Deutschland
- Ecuador
- Eesti
- España
- France
- Hong Kong SAR
- Hrvatska
- India
- Indonesia
- Ireland
- Italia
- Latvija
- Lietuva
- Magyarország
- Malaysia
- México
- Middle East
- Nederland
- New Zealand
- Nigeria
- Norge
- Österreich
- Pakistan
- Paraguay
- Perú
- Philippines
- Polska
- Portugal
- Puerto Rico
- România
- Saudi Arabia
- Singapore
- Slovenija
- Slovensko
- South Africa
- Sri Lanka
- Suisse
- Suomi
- Sverige
- Switzerland
- Türkiye
- United Kingdom
- United States
- Uruguay
- Venezuela
- Việt Nam
- Ελλάδα
- България
- Казахстан
- Србија
- Україна
- ישראל
- الشرق الأوسط
- المملكة العربية السعودية
- ไทย
- 中华人民共和国
- 臺灣 地區
- 日本
- 香港特別行政區
- 한국
- Recalls|
- Product recycling|
- Accessibility|
- CA Supply Chains Act|
- Privacy|
- Use of cookies|
- Your privacy choices|
- Terms of use|
- Limited warranty statement|
- Terms & conditions of sales & service|
©2025 HP Development Company, L.P. The information contained herein is subject to change without notice.